Wertschöpfungs-Optimierung
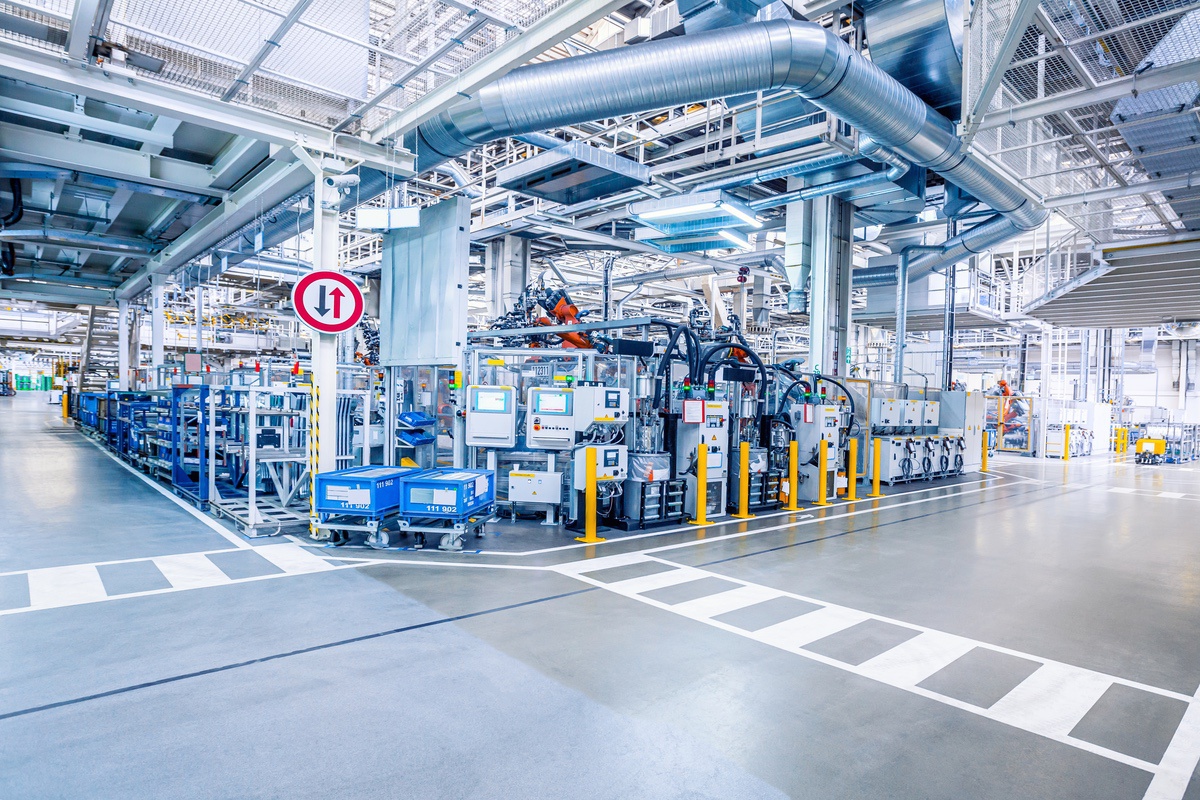
Ausgangssituation
Unser Kunde ist ein global agierender Marktführer für die Entwicklung, Fertigung und Montage von Turboladern. Aus diversen Standorten werden alle großen OEM sowie der Markt für Nutzfahrzeuge versorgt. Vor dem Hintergrund stetig steigender Anforderungen an die Flexibilität in der Produktionsplanung, die Lieferfähigkeit und die Verfügbarkeit von spezifischen Produkten, galt es vor allem den zentralen deutschen Standort neu zu organisieren.
Ziele
- Steigerung der Leistungsfähigkeit in der Produktion > 30%.
- Eliminierung von Lieferrückständen Stabilisierung der Produktion
- Flexibilisierung der Auftragslose
Beschreibung der Aufgabe
Einführung von Lean Produktion von der Analyse des alten Systems bis zur Stabilisierung der Serienproduktion in den neuen Strukturen.
Übernahme von Verantwortung im Sinne der Projektleitung sowie der Übernahme von Interims Management Funktionen.
Umbau des Werkes bei laufendem Betrieb sowie unter intensiver Einbindung der vor Ort tätigen Mitarbeiter. Enge Abstimmung aller Aktivitäten mit Kunden, Dienstleistern, Lieferanten und zentralen internen Einheiten. Permanentes Reporting an die Geschäftsführung.
Auszug einiger Schwerpunkte
- Analyse des Produktportfolios im Sinne von Mengen, Kundentakt, Arbeitsinhalte, Wertschöpfungsketten, Technologien, Planungsprozesse und Rüstvorgänge.
- Ableitung von Kriterien, für die Entwicklung von Standardlinien. Ausplanung dieser Linien – im Hinblick auf Hallenlayout, Anbindung an die Materialversorgung, die Gestaltung der Werkbänke bis zur Feinsteuerung der Aufträge. Realisierung einer Pilotlinie inkl. Freigabe zur Serienfertigung durch den OEM
- Verlagerung von Anlagen, Maschinen und Montagelinien. Umbau der Hallen – neuer Fußboden inkl. Markierungen, neue Energieversorgung, neue Beleuchtung, …
- Einbindung der Linien in die Strukturen des Werkes. Realisierung einer völlig veränderten Logistik – KANBAN Steuerung; Routen-zügen, One piece flow, durchgängiges Behälter Konzept, …; Tracking der Performance.